The Goldbeater, the Cow and the Airship
01. May. 2006
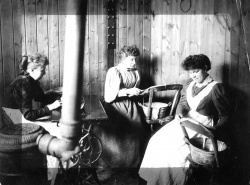
A rare picture from c. 1900 shows the production of gold beater's skin. Photo: Royal Engineers Library, UK
Exterior Skeleton
The airships that were associated with the golden age of airship travel, which ran from the 1910's up to 1940, were essentially constructed from one large frame. The now classic airship cigar shape is the shape of this large frame, called a hull. The hull and everything within, were protected from the elements by canvas that was stretched over the hull and painted with an aluminium paint, for added protection. This is the outer most character of the zeppelin, it's public-face. Being 245 meters long, this public face was impressive (as any public face should be)! But this huge hull was merely the frame around the gasbags, for it was the gasbags themselves that did the very real job of actually floating the zeppelin.
A Volatile Lifting Gas
Usually around seventeen to twenty gasbags were used in a single airship, all of which were con-tained in the hull. Each one filled with the hydrogen would in turn float the airship. It seems unfeasible, perhaps even impossible, that a 245 meter long structure weighing up to 230 tons, could be rendered lighter than air. But it was the unique and extra ordinary quality of hydrogen, being the lightest element in the universe, as well as the equally unique and extraordinary quality of the gasbags themselves that enabled this.
Hydrogen is the lightest element in the world because it has the least amount of particles, in fact it has just one particle. Whilst technically speaking there are tiny traces of lots of elements in air, it is mostly made up of two elements, Nitrogen and Oxygen. Nitrogen has fourteen particles and oxygen has sixteen. Quite simply, this means that hydrogen is at least thirty times less dense than air! Used as a lifting device its lightness was powerful enough to lift the several hundreds of tons of airship into the air. But having only one particle means that hydrogen tends to leak through every thing it is con-tained in. As a result the construction of the gasbags inside the airships is one of the most intricate processes associated with the whole airship subject.
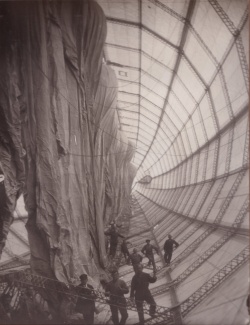
From the building of the airship "Bodensee", 1919. The empty gas bags are hanging from the frame in the hull of the airship. Photo: Archiv der Luftschiff-bau Zeppelin GmbH.
Flying Blind Guts
The gasbags themselves are made from a material called goldbeaters skin. It is a curious material that involves a long, mysterious and once secretive, process of manufacture. The use of Gold leaf reaches back through time with some of the earli-est examples of gold leaf found amongst the shim-mering sarcophagi of the Egyptian Pharaohs and on Greek pottery dating from the 4th century BC.
The process of making gold leaf these days in-volves precision rolling machinery but this is a relatively recent thing. Until the 1960's gold leaf was made entirely by hand. Whilst there is no evidence of the technique earlier than the 15th Century, it is believed that the techniques used for the adorn-ment of the Pharaohs' sarcophagi did not differ significantly to those used in the 20th century.
The gold leaf would be beaten from a small ingot of gold. This would involve sandwiching the gold be-tween a kind of vellum or skin, aptly called gold-beater's skin. The process would continue until a pack of 500 gold leaves was created with each leaf separated from one another by the protective gold-beater's skin. The finished gold leaf was an unimaginable 0.000125 mm thick! To produce a piece of gold leaf in this way is an incredibly skilled task and goldbeaters would pass their cherished skills down through the family. It was the goldbeaters themselves who knew how to make the skin, which involved a similarly secretive and coveted technique. As such the process and ingredients involved were seldom written down.
Goldbeaters skin is made from part of a cows intestine, the outer layer of the caecum to be precise, which is also called blind gut or even the appendix. The outer layers of the blind-gut are carefully stripped off into sheets of around 60 cm in length by 25 cm in width. They are then cleaned of fat by dipping the gut in a mild alkaline solution and scraped with a blunt knife. The cleaned gut is then stretched over a frame. One quite remarkably quality of this material is that separate sheets can be joined or welded when wet by carefully rubbing the overlap of the two sheets. Several layers can be made this way as well, for example, airship gasbags usually consisted of up to seven layers of skin.
The living tissues in the sheets grew together making a seamless and Hydrogen proof join. As well as being impermeable to Hydrogen it was also light and very strong, making it the perfect gasbag material! However it was very labour intensive and time consuming to produce. Supply of goldbeaters skin ran out during the First World War, forcing the Zeppelin Company to recycle the material from older airships as well as use an inferior artificial substitute for the construction of the gasbags. The poor quality of these wartime gasbags were considered responsible for the loss of many war-time airships and their crew.
Incredible Quantities
Airship gasbags were big things! For example, Hindenburg had a gas capacity of nearly 212,000 cubic meters. So it becomes clear that these sheets, each one being painstakingly prepared by hand and fused with each other and done so in many layers, were also required in unimaginable quan-tities. Moreover, when only two sheets could be obtained from the intestine of one cow, we realise that an awful lot of cows were required to service the demands of the airship industry!
In reality, the gut was obtained as a by-product of the meat industry. But over 200,000 sheets of gold-beaters skin were needed for the gasbags of a standard German naval airship that was used during World War One. But this type of airship was small in comparison to later models. The American mili-tary airship U.S.S. Shenandoah used 750,000 separate sheets of goldbeaters skin for its gasbags. These are mind-boggling quantities! However, without wanting to confound the confounded, the gas-bags of Hindenburg were over three times the capacity of the gasbags of the U.S.S. Shenandoah!
Goldbeaters' skin seems an incongruous technology to be found associated so closely with the air-ships that were themselves so stylish and symbolic of the future, of science and of technological brilliance. The mysterious technology and culture associated with the production of this material, which in itself has strange qualities, seems more akin to the black arts and to hokum than to cutting edge technology, and seems almost brutish next to the effortless serenity it afforded the airships.
Goldbeaters' skin does seem to amply denote the superficiality of the airships iconic status seems, a status that appears to have been only skin deep. The intriguing subject of the goldbeaters' skin may in itself also add to the continuing and lasting mystery and fascination that the airships continue to com-mand. However, it seems an absurd reality that what actually kept this vision of the future afloat was a technology that predated the birth of Christ!
This article may be copied or quoted with MuseumsPosten, Post & Tele Museum as source.
Comment this article
Only serious and factual comments will be published.